Cruisette: Builders' Diary
Ron & Devy Porter
Continued
As I said, the basic boat is 15 feet long, but
there is an architect's note stating that lengthening by 10% to 16.5 feet
is permitted through the simple expedient of increasing the frame spacing
accordingly. That is but one of the customizations planned, although we're
not going to get too crazy with things that affect the weight, balance, or
handling. Since the architect rates the 15-footer as capable of handling a 60hp
motor, I think that we'll try to go to that. Lenthening it a bit should
increase the power it can take, but the performance characteristics with 50hp
on 15ft sounded pretty good, so 60hp on 16.5 ft should be OK. And I don't
think we can afford anything more powerful anyway :) [Update: due to the fact
that the stem was pre-cut as for a 15 footer, we've had to scale back
slightly to an estimated 16 feet].
We live in an apartment so we had to find a shop.
Fortunately, I work for a great company, Crestline Coach Ltd.,
and they graciously allowed us to use a corner of one of their buildings as a
shop. In addition, the R&D manager is going to help source the aluminum for
the trailer--and do the welding! Crestline's main line of business is the
construction of custom ambulances, most based on all-aluminum bodies designed
and constructed on-site, so neither materials nor expertise will be hard to
come by!
Building jig
The building jig has some special considerations,
given the constraints on the workspace. Crestline is gracious enough to provide
building space and technical expertise in building the trailer, but can't
guarantee a fixed location within the building. After all, the space is under
construction as their powdercoat facility. Still, the demands of creating a
mobile building jig make for some challenges. The basic plan is to take a
leftover 16-foot pallet (Crestline gets pallet-loads of 16-foot aluminum
sheets) and sheet it top and bottom with leftover MDF (protective underlay from
the CNC router tables). That, in combination with some 2x10's or similar on
edge should create a rigid platform on which to mount the jig. And with luck,
we won't have to move until the hull is sheeted in!
Day One ( Dec 10, 2005): Well, we're getting started at last!
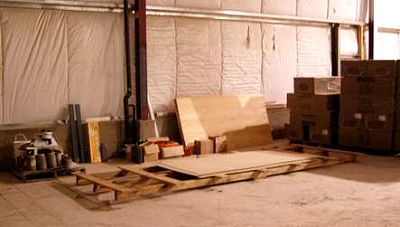
Here is the workspace. It's a little shy on light, but
we should be OK.
In the foreground, you see the 16' x 6' pallet and
the MDF that will serve as our mobile building platform. It's a little
bouncy on one end (the left), but that should stabilize nicely once we get
under way. In the worst case, we'll just shim that end up a bit.
In the background you see some of our materials, tools, and
general stuff. The extreme right and left is just stuff that Crestline needs as
part of constructing their powdercoat facility. Get used to seeing various and
sundry odd bits hanging around the edges.
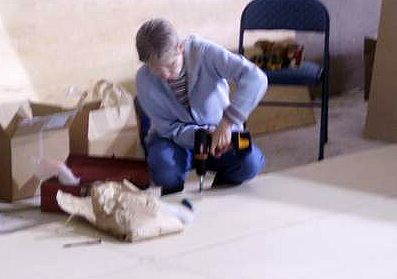
Here's a shot of Devy driving one of the approximately
50 screws it took to fasten the MDF to the pallet. She's a little uncertain
right now, but she'll be an expert by the time she's helped to drive
the hundreds it takes to hold the boat together. Our experience with sheeting
in the building platform led us to pick up another cordless drill/screwdriver,
and we'll probably make yet another trip to pick up a couple of spare
batteries. The things we do to avoid tripping over cords!
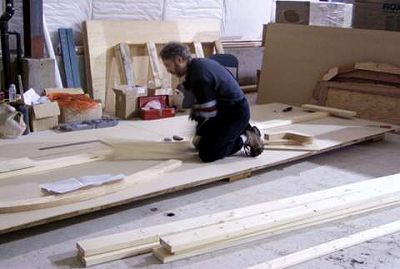
Here's one of me working on the beginnings of the
building jig. At the far right, you can see some of the boat frames and to the
left you can see the plans for the jig and the boat's 'stem' (the
part that defines the rounded curve up front). I had to dig out the frames
earlier than I planned in order to figure out just what room there was for
lengthening the boat. Since the stem is pre-cut based on a 15' length,
there is no way to increase frame spacing in the front 6' of the boat.
Thus, instead of getting an extension of 18" (to 16.5'), we're
only going to get 16' overall. Oh well, I'm quite sure that we'll
appreciate the extra foot we'll be getting and the 6" we won't see
we can't miss.
Day Two ( Dec 11, 2005): The framing jig is finished!
Well, we got the framing jig finished. It took us a
total of about 8 hours, including a false start on the length. As were were
setting up the jig, I got confused with regard to frame spacing requirements
given the intial desire to make the allowed 10% lengthening. Basically, I
misremembered the actual wording of the architect's notes. I thought that I
had to increase the spacing of all frames. In fact, the actual wording states
that the length can be increased by 10% by increasing the relative spacing of
all frames aft of the stem. I had that set up, although only 12 inches worth
because I thought I was 'missing' some room to move because of the
pre-cut stem. Graham Knight, on the Glen-L Builders' Forum pointed out the
error of my ways, but not before I chickened out on what I though was an
unapproved design change. In the end, I feel much more relaxed about where
we're going for the simple reason that I don't have to worry about
missing something related to an increased length. We weren't planning to
increase the size of the cabin, so all the space would have been gained in the
cockpit, an area that really doesn't benefit that much from increased space
given our planned usage. To be honest, I don't know that I even had a good
reason for wanting to go longer. Anyway, on with the show...
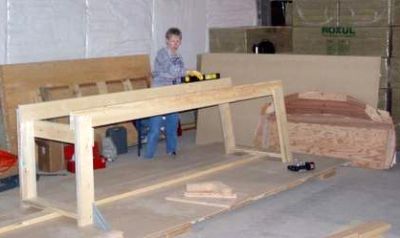
Here's Devy double-checking that things are level. We
found getting things straight, square, and level to be a bit of a challenge,
but it was more nit-picky stuff than difficult or confusing stuff. In the end,
we're straight, square, and level, so we must have done something
right.
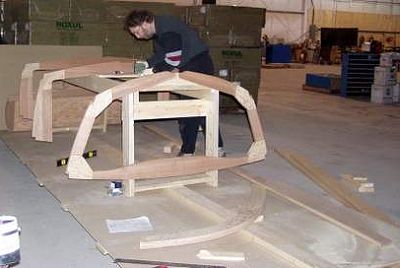
Here I am working on centering frames over the building jig.
The frame in the foreground is at station 2 and presented a few challenges.
According to the plans and building instructions, the 'floor timber' is
supposed to rest on the 'setup members' (the long stringers). Either
I've goofed again already, or somebody at Glen-L has a bug in their plans.
The plans call for the jig to have a spacing of 28 inches between the uprights.
The setup members are 2x6 and are fastened to the inside of the uprights. The
floor timber of frame 2 is 24 inches long. Sorry folks, but the gap between the
setup members is 25 inches! Anyway, I just took a piece of scrap and added a
little table for the floor timber to rest on.
Next issue: Framing the hull
|