Inboard Hardware: Making the Shaft Hole
Page 2...
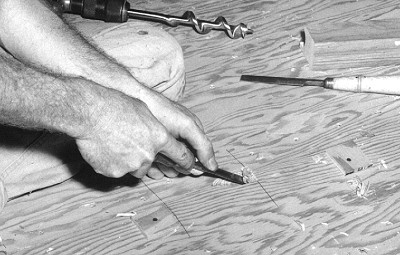
FIG. 12-1: A cleft is made with a chisel at the point
where the centerline of the shaft will start through the planking. The depth of
the notch should be equal to the radius of the hole to be drilled. With a
gouge, cut an arc to allow the auger to be inserted.
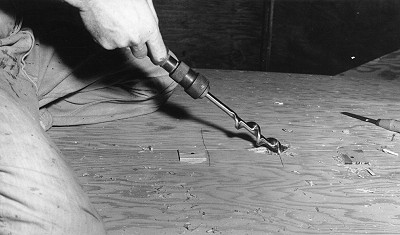
FIG. 12-2: The hole to be drilled is generally large
enough to allow at least 3/8" overall diameter clearance. With a 1"
shaft, for example, a 1 3/8" shaft hole would be bored. Some builders
prefer not to use an auger as the point tends to track with the grain. The same
would hold true for an expansive bit. A ship's auger or a
"barefoot" auger are better, especially if the hole is long. A drill
with a welded-on extension could also be used. The hole is bored by starting
the drill in the cleft point, after removing all fasteners that may be in the
way of the shaft hole.
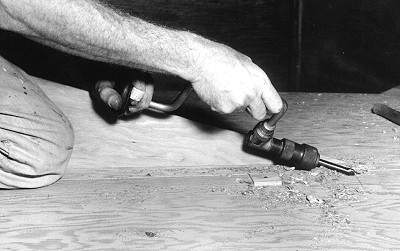
FIG. 12-3: By gradually bringing the drill down as you
drill, the hole can be bored at the proper angle. Note that the template taken
from the layout is used to determine the proper angle. One person drilling, and
another checking the angle, will help assure the correct alignment.
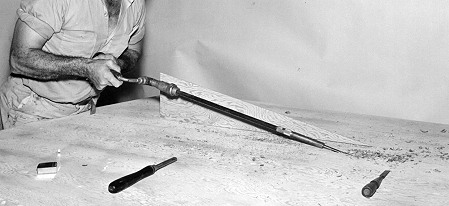
FIG. 12-4: When the shaft angle or hole is long, an
electrician's extension for the drill can be used. If a block of wood is
fastened inside of the boat, the hole can be cleanly drilled, without
splintering on the inside.
Continue
|